AUTOMATION MAKES LIFE BUTTER
September 10, 2021
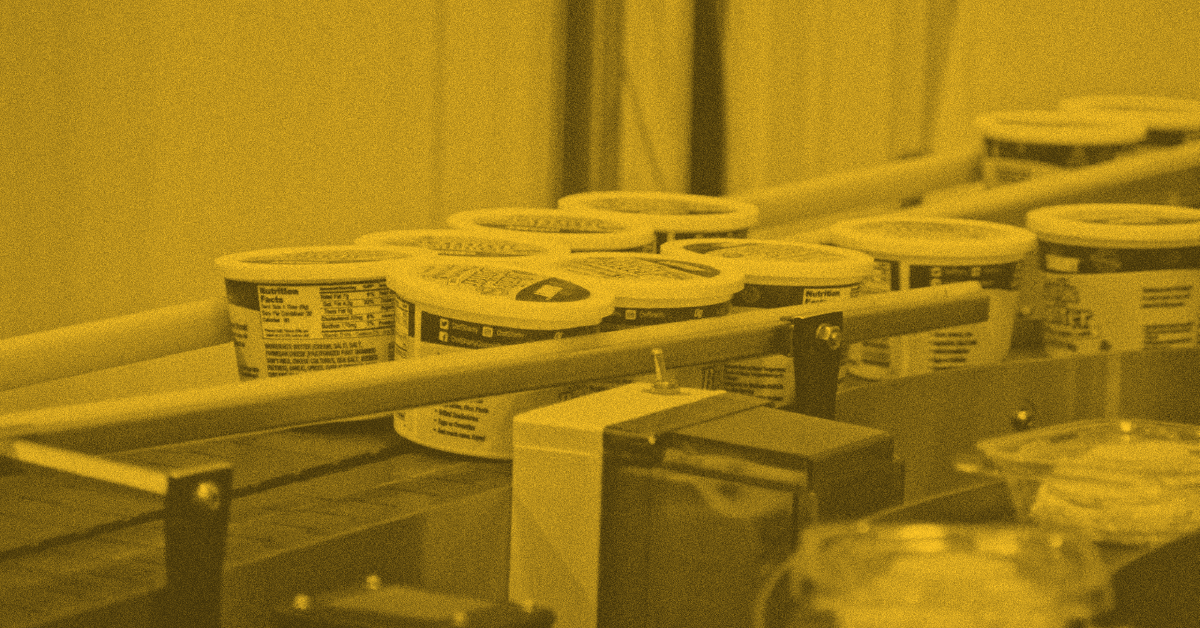
DON’T HESITATE. AUTOMATE.
AI is making its way into warehouses more and more—and we’re not mad about it. We’re always looking for ways to help our customers innovate smartly. That’s what makes our partnerships unstoppable. And when you throw Robocop into the mix, it gets even more bulletproof. Because there’s an endless number of opportunities and solutions, like automated packaging.
In fact, it was automation that our longtime client Chef Shamy needed.
This artisanal butter manufacturer went from serving the family to serving the nation. Their gourmet butter can now be bought at huge stores like Costco, Sam’s Club and Walmart. But with that success came a serious question for Chef Shamy: How do we keep up with demand?
FEWER COOKS IN THE KITCHEN. BUT MORE MACHINES.
Equipment design and implementation isn’t new for Ernest. We’ve used this solution to help other customers thrive, including Boston restaurant Spyce with their automated robot pal named Flippy. We also helped Boman Kemp keep things running smoothly with their ring-shaped stretch-wrapping machine. So, we knew automation would be a great opportunity for Chef Shamy. And after a lot of research, vetting and collaboration, we realized that simplifying the packaging process with automated equipment was key.
Chef Shamy’s existing packaging system only allowed the company to run its production line at 40-50% capacity, with each packaging line requiring 4-6 people at the backend to hand-pack the butter into boxes and put them on rotating tables.
Simply put, there were too many cooks in the kitchen. But there was room for a machine—a Combi machine.
MORE BUTTER = MORE HAPPY STOMACHS.
Despite being rolled out during the midst of Covid-19, the Combi machine proved successful—partly due to both the Combi and Ernest teams being on hand for installation and training, in addition to answering questions.
Since the installation, the Chef Shamy team has doubled its production capacity with room to grow. Compared to previous run rates of 40-50% capacity, production now ranges from 75-80%. When you couple that with a 61% increase in overall productivity, it’s easy to see the effect this humble but hardworking robot brought to the table.
While the majority of the Chef Shamy team runs other aspects of the business, it only takes one team member per line to monitor the Combi machine as it forms the boxes, fills them with butter tubs and adds stickers and seals the lids.
Read more about our solution for Chef Shamy here.
PRETTY TASTY NEWS.
The good news with automation doesn’t seem to end…which is perfect for us (and you) because who likes bad news? (Answer: no one).
With automation, productivity improves. By assessing your line design and layout, you can discover what’s causing the inefficiencies and production delays. Then, by implementing the right machine or machines, you can keep up with the increased demand without increasing the size of your team.
Another pro? A stellar reputation. Automation allows businesses to gain a deeper understanding of their operations—which can lead to stronger market strategies. Not to mention a leg up (or automated arm) on the competition.
Here’s one more perk for good measure…fewer mistakes are made. Robots are more precise than humans, especially when it comes to the, well, robotic work. These tasks can be carried out more accurately and faster, without the risk of repetitive injury or unnecessary fatigue for your team.
So, what are you waiting for? Let’s get talking! If you’d like to learn more about how automation can help your business grow, head to ernestpackaging.com/contact to speak with an Ernest Packaging representative.